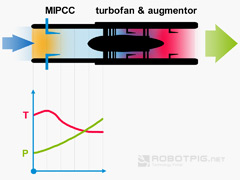
MIPCC (Mass injection pre compressor cooling) is a system that injects water and liquid oxygen to a turbofan/jet's inlet. Turbojets sustain a drop in their efficiency as the atmospheric pressure decreases (in higher altitude) and the air temperature rises (high airspeed).
With the water injection the air temperature is substantially lower and the additional oxygen helps to stabilize the flame front (especially inside the afterburner)
This system has the advantage of increasing the performance without sacrificing the engines life or reliability because it just simulates the operating conditions of lower altitudes.
An aircraft equipped with MIPCC turbojets flying at 100.000ft at 3.0 mach has operating conditions at its engines similar to those flying at sea level. With the appropriate aircraft conventional turbojets with MIPCC can operate at speeds that reaches 6 mach.
This system can be disengaged easily in lower altitudes where the engine doesn't benefit from its function.
Tests have taken place in the US by applying similar systems in J57 and J75 engines and the Soviet Union used water and methanol injection in the high altitude 2.8-3 mach MiG-25.