The first rockets where simple tubes with a hole from which the detonation of gases produced the thrust. This primitive design exploits only the reaction and a large amount of energy from the plume expansion is wasted. The purpose of a rocket nozzle is to convert the largest possible amount of energy from the fuel burn to thrust.
The bell shaped nozzle is maybe the most popular. It has a parabolic (or similar) intersection and its shape converts the pressure front from the gas expansion to a reactive force (thrust).
There is an optimum nozzle shape for every external atmospheric pressure (which is mostly a function of altitude). In higher altitude (lower atmospheric pressure) the nozzle is too small for the plume and in lower altitude (higher atmospheric pressure) the exhaust plume is distorted from the higher-pressure ambient air that enters inside the nozzle. The nozzle dimensions and shape for a vehicle that will travel in various pressure conditions is a compromise.
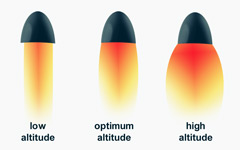
One solution to this problem is the aerospike nozzle with its inherit altitude compensation. You can trace its design in the following graph. One derivative of the conventional bell shape nozzle is the annular nozzle. An assymetrical derivative eliminates the outer wall and retains a long central spike that emulates a very long nozzle.
The long spike can be replaced with an abrupt cut and produce a compact setup. This may have a small penalty performance-wise in comparison to a full spike but it is much more compact and more efficient than a conventional bell shaped nozzle of the same size.
It operates by exploiting a secondary subsonic recirculating flow at the base of the central 'spike'. This flow acts like a conventional spike and it increases substantially the nozzles performance. A small bleed at the base can also increase the performance almost at a full-length spike's level.
A big advantage of the aerospike nozzle is that by using the atmospheric pressure as a virtual outer wall it has inherent altitude compensation capabilities. The flow is adjusted naturally to the ambient conditions and the overall performance of the nozzle stays close to the optimum.
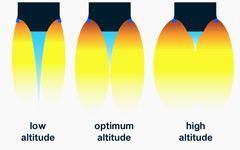
Its main disadvantage is the much higher complexity and a small weight penalty. However it can be easily integrated to the vehicle and it can be modular in a linear arrangement.
The most advanced aerospike engine is the P&W XRS-2200, destined for the X-33 and later for Venture Star spacecraft, both cancelled. The XOV vehicle mentioned in the article was supposedly designed around a linear aerospike engine.