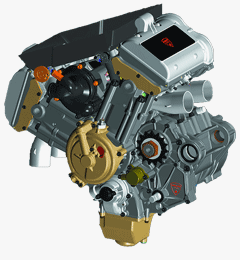
In conventional valvetrain systems the rotating camshaft pushes the valve downwards and simultaneously compresses the valve spring. This spring is used to reposition the valve in the closed position by its expansion.
In desmodromic systems every camshaft has two lobes per valve. One is used (as in conventional systems) to push the valve downwards in the open position and the other lobe is used to reposition the valve in the upward - closed- position.
Desmodromic valvetrains in effect replaces the valve spring with a second lobe.
In the following image you can see on the left a conventional valve-spring system and on the right a desmodromic.
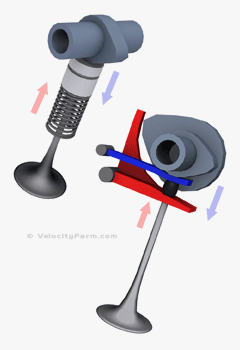
The blue arrow in both cases indicates the cam lobe that provides the downward movement and opens the valve. In the desmodromic system the camshaft operates via the blue element, a rocker arm, which is articulated and follows a circular path. The red arrow indicates the upward movement that closes the valve. This movement is provided either by the expansion of the valve spring or by the red element. This rocker arm is placed under the top of the valve stem and provides the lift by following the movement of the second lobe.The blue arrow in both cases indicates the cam lobe that provides the downward movement and opens the valve. In the desmodromic system the camshaft operates via the blue element, a rocker arm, which is articulated and follows a circular path. The red arrow indicates the upward movement that closes the valve. This movement is provided either by the expansion of the valve spring or by the red element. This rocker arm is placed under the top of the valve stem and provides the lift by following the movement of the second lobe.
Desmodromic systems provide a more accurate control on the valve movement. Given the correct adjustment of the system the valves should follow the exact orbit designed by the engineers. They can open and close for as long and as sudden as required. There is also a power advantage because springs consume some energy to contract every time and also desmodromic valvetrains can operate in high rpms because there isn't any spring inertia.
Conventional engines require very hard springs in order for them to follow the movement of the valve in high rpm but apart from the limit of such a layout, hard springs increase the power losses.
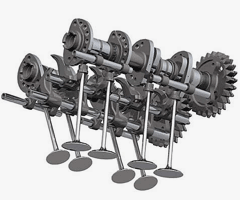
The main disadvantage of desmodromic valvetrains is the increased in complexity their design requires and the high maintenance and frequent readjustment they need.
Advances in metallurgy and conventional valvetrain technology almost consist their advantages obsolete because we can have conventional engines of similar performance.
It is a respectable, if somehow exotic, technical solution though.
Another system that eliminates the conventional valvetrain problems is the pneumatic valvetrain system, which is used in Formula 1 engines. This uses air springs with variable preload and characteristics and such engines are capable of very high rpm operation.
Pneumatic valvetrain had been used in MotoGP by the Aprilia RS3 Cube in the past.